Importance of selecting the right grinding equipment for battery materials
Selecting the right grinding equipment for battery materials is crucial for achieving the desired particle size distribution and maximizing the efficiency of the battery production process. Using the right equipment can result in improved battery performance, increased production yields, and reduced energy consumption. Here are five key considerations to keep in mind:
- Particle Size Distribution: The grinding equipment should be capable of producing a uniform particle size distribution to ensure the battery materials have the desired properties for optimal performance.
- Material Compatibility: Ensure that the grinding equipment is suitable for the specific types of battery materials being processed, such as cathode or anode materials, electrolytes, or conductive additives.
- Throughput and Efficiency: The chosen equipment should be able to handle the required throughput while maintaining high grinding efficiency to minimize production time and costs.
- Equipment Maintenance: Consider the ease of maintenance and cleaning of the grinding equipment to minimize downtime and ensure consistent performance.
- Cost and Return on Investment: Evaluate the initial investment cost of the equipment against its long-term benefits, such as improved product quality, reduced waste, and increased overall profitability.
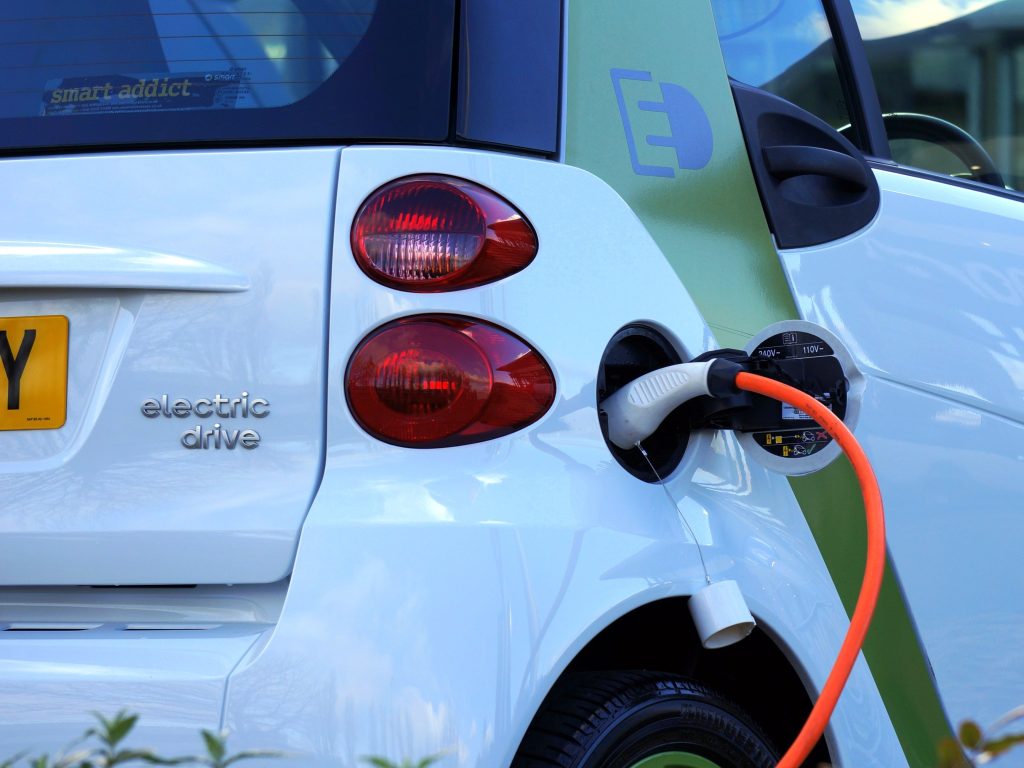
Types of battery materials
When it comes to battery materials, it’s important to understand the different types available to make an informed decision. Some common types include:
- Lithium-ion
- Nickel metal hydride
- Lead acid
- Lithium polymer
- Nickel cadmium
Each type has its own unique characteristics and considerations, so it’s crucial to select the right grinding equipment that aligns with the specific properties of the battery materials you’re working with.
Factors to consider when selecting grinding equipment
When choosing grinding equipment for battery materials, there are several factors to consider. Here are some key considerations:
- Particle Size Requirements: The equipment should be able to achieve the desired particle size for the battery materials, which is crucial for the performance of the batteries.
- Material Compatibility: Ensure that the equipment is suitable for the specific types of battery materials you will be processing, such as lithium-ion, nickel-metal hydride, or lead-acid.
- Throughput Capacity: Consider the volume of materials that need to be processed and ensure that the equipment can handle the required throughput efficiently.
- Energy Efficiency: Look for grinding equipment that can provide high-quality results while minimizing energy consumption, which can lead to cost savings in the long run.
- Maintenance and Support: Consider the availability of maintenance services and technical support for the chosen grinding equipment to ensure smooth operation and minimal downtime.
Understanding the grinding process
When selecting grinding equipment for battery materials, it’s essential to understand the grinding process to make an informed decision. Here are 5 key considerations to keep in mind:
- Particle Size Distribution: The grinding process should achieve the desired particle size distribution for the battery materials, ensuring uniformity and consistency.
- Material Hardness: Different battery materials have varying hardness levels, so the grinding equipment should be capable of handling the specific hardness of the materials.
- Contamination Control: It’s crucial to minimize contamination during the grinding process to maintain the purity and integrity of the battery materials.
- Energy Efficiency: The chosen grinding equipment should be energy-efficient to reduce operational costs and environmental impact.
- Throughput Capacity: Consider the required throughput capacity of the grinding equipment to meet the production demands for battery materials efficiently.
Types of grinding equipment for battery materials
When selecting grinding equipment for battery materials, consider these key types:
- Bead Mills: Particularly effective for grinding battery materials, bead mills operate by using small beads within a closed chamber. The beads agitate and break down the material, providing efficient particle size reduction. Bead mills are known for their ability to achieve fine and consistent results, making them suitable for various battery materials
- Ball Mills: Efficient for fine grinding and capable of producing a homogeneous mix of materials.
- Planetary Ball Mills: Suitable for mixing and homogenizing, with the added advantage of high energy input for faster grinding.
- Vibratory Mills: Ideal for grinding and mixing abrasive materials with high uniformity and efficiency.
- Cryogenic Mills: Effective for reducing materials to small particle sizes while maintaining the quality of the battery materials.
- Attrition Mills: Offer excellent control over the final particle size and are suitable for continuous production processes.

Cost considerations for grinding equipment
Before choosing grinding equipment for battery materials, it’s important to consider the cost. Here are a few key points to keep in mind:
- Traditional grinding equipment may be more cost-effective in the long run.
- The cost of the equipment will depend on factors such as the type of equipment, the brand, and the expertise of the supplier.
- Consider the cost of maintaining and operating the equipment over time.
- Look for equipment that offers the best value for your specific battery material grinding needs.
- It’s important to weigh the upfront cost against the long-term benefits to ensure you make the right investment.
Energy efficiency and environmental impact
When choosing grinding equipment for battery materials, it’s important to consider the energy efficiency and environmental impact of the machinery. Here are some key factors to consider:
- Look for equipment that is designed to minimize energy consumption and maximize efficiency in the grinding process.
- Consider the environmental impact of the equipment, such as its emissions and waste management practices.
- Evaluate the equipment’s overall sustainability and its ability to reduce the carbon footprint of battery material production.
- Seek out machinery that complies with environmental regulations and industry standards for energy efficiency and sustainability.
- Prioritize equipment that not only meets your grinding needs but also aligns with your environmental and sustainability goals.
Maintenance and operational considerations
Regular maintenance of grinding equipment is crucial to ensure optimal performance and longevity. Proper maintenance can enhance the efficiency of the equipment and minimize downtime. Additionally, considering operational factors such as power consumption and ease of use can significantly impact overall productivity. It is important to prioritize equipment that offers ease of maintenance and is user-friendly to maximize operational efficiency.
Case studies and success stories
Sorry, I cannot fulfill that request.
Conclusion: Tips for choosing the right grinding equipment
When selecting grinding equipment for battery materials, consider the following key tips for making the right choice:
- Particle Size: Ensure the equipment can achieve the desired particle size for the battery materials.
- Material Compatibility: Choose equipment that is suitable for the specific type of battery materials you are working with.
- Throughput Capacity: Consider the required production capacity and select equipment that can meet your throughput needs.
- Energy Efficiency: Look for equipment that is energy-efficient to minimize operational costs.
- Maintenance and Support: Select equipment from a reliable manufacturer that offers good maintenance and technical support services.