Introduction to High-Precision Grinding in Battery Material Development
High-precision grinding kicks battery material performance up a notch. Why? Because the finer and more consistent the particles, the better electricity zips through your battery. Think of it like a highway; smoother roads allow for faster, safer travel. It’s the same for electrons in a battery. Precision grinding ensures particles are the right size and shape, which means they can pack together just right—no wasted space. That’s essential for denser, more efficient batteries. Plus, it also helps batteries charge faster and last longer. So, whether it’s for your smartphone or electric car, high-precision grinding has a huge role to play in getting those longer-lasting, quicker-charging batteries we all want.
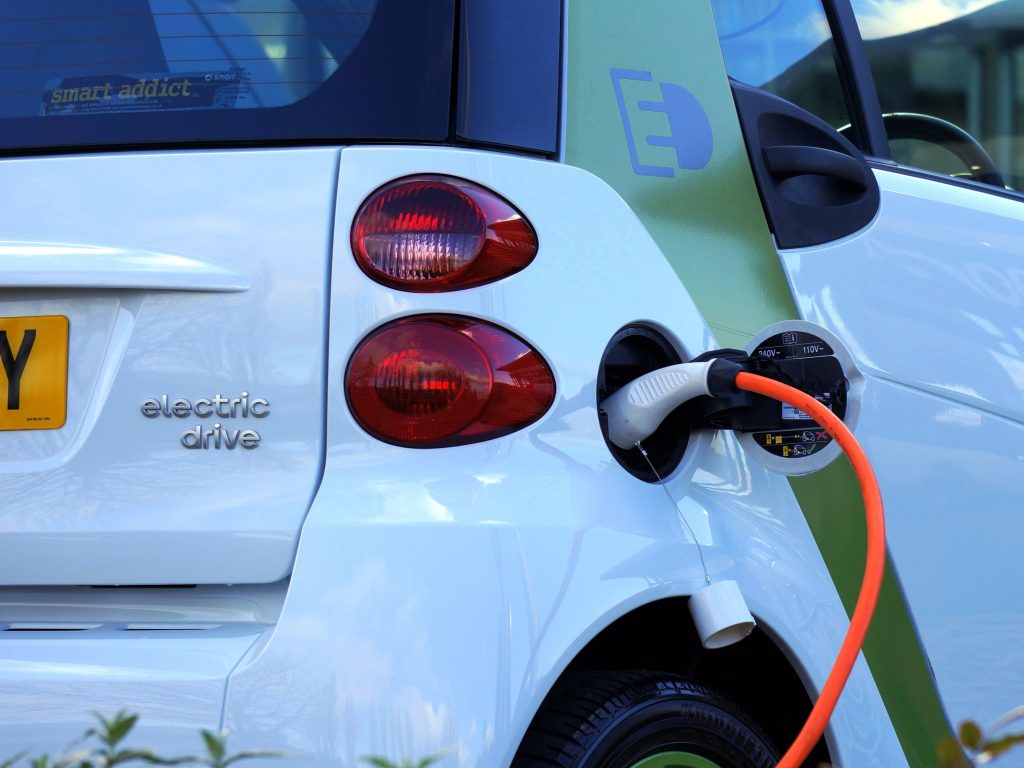
Understanding Battery Materials: Types and Characteristics
In the realm of battery materials, two main types take the spotlight: cathode and anode materials. Let’s not get tangled in jargon; simply put, cathode materials are the lifeblood of a battery’s positive side, while anode materials ground the negative side. For cathodes, you’ll often hear about lithium cobalt oxide or lithium iron phosphate, boasting high energy density or safety, respectively. Then, graphite reigns as a common anode contender, prized for its stability. These materials greatly influence a battery’s performance, lifespan, and safety. Thing is, they need to be ultra-fine and consistent to do their job well—enter high-precision grinding, a process that ensures these materials are the right size and quality, laying the groundwork for batteries that are not just robust but also reliable.
The Importance of Material Fineness in Battery Performance
Getting the material just right is key for battery performance. See, high precision grinding turns raw materials into fine powders with particle sizes so small you might never see them if they were on your fingertip. This fineness is crucial—it decides how well the battery conducts electricity and how much power it packs. If the particles are too big or uneven, the battery can’t work as efficiently, which might mean your smartphone dies faster or your electric car doesn’t go as far on a single charge. Manufacturers use fancy grinding machines to make sure everything’s the right size, which helps in making batteries that are not only powerful but also long-lasting and reliable. Bottom line—finer materials make for better batteries.
Advances in Grinding Technology for Enhanced Battery Materials
Grinding technology has gotten real good. It’s shaping the future of batteries that power your gadgets, cars, and even homes. Think of grinding like a high-precision dance, where machines and materials move in sync, crushing down particles to insanely small sizes. That’s how scientists are making battery materials better. These tiny particles have a big job. They help batteries store more energy, charge faster, and last longer – a real game-changer. Plus, smarter grinding means fewer rough spots in the materials, so your batteries work like a dream. As grinding gets even more advanced, expect to see batteries stepping up their game. Cool, right?
How High-Precision Grinding Affects the Lifecycle of Batteries
High-precision grinding is crucial in producing battery materials that are not only effective but durable. Think of it like this: if you want your car to run smoothly, every part needs to be made just right. The same goes for batteries. Grinding the materials to exact specifications ensures a consistent size and shape, which leads to better performance and a longer life for your battery. When particles are uniform, you get a more reliable reaction in the battery, and that means your phone or electric car won’t quit on you when you need it most. In short, the care taken in grinding the materials translates directly to how well the battery works over time. So, good grinding equals a longer-lasting battery.
The Role of Particle Size and Distribution in Battery Efficiency
When it comes to battery materials, size really does matter — we’re talking about the particles here. The particle size and how evenly they spread out, known as distribution, can make or break a battery’s performance. Smaller and uniform particles mean batteries can charge faster and last longer.
You see, with smaller particles, the ions inside the battery have less ground to cover. This means they can dash from one side of the battery to the other more swiftly, giving you a quicker charge. Plus, small particles pack together more tightly, which makes for a denser, more stable battery compound. Uniform particles ensure that the reaction inside the battery happens efficiently and consistently, so the power output stays smooth and reliable.
In short, getting the particle size and distribution right is like having all the dancers nail their moves perfectly in a choreographed routine — when everything syncs up, the performance is top-notch. With batteries, that means your phone won’t die right when you’re about to win the game or snap that perfect photo. That’s why high-precision grinding, the process that shaves those particles down to just the right size and spreads them out just right, is key in the battery material game.
High-Precision Grinding Equipment for Battery Material Processing
High-precision grinding equipment is key for shaping battery materials into the fine powders necessary for high-performance batteries. These machines achieve particle sizes with such precision that they ensure uniformity and quality, which are crucial for battery efficacy and lifetime. The precision also allows for better control over the material’s chemical properties, essential for battery stability. These grinders must be both powerful and accurate, able to handle materials like lithium, cobalt, and nickel without contaminating them. By using high-precision grinding, manufacturers ensure that when you charge your devices, the power you get is reliable, lasting, and efficient. This isn’t just grinding; it’s paving the way for the next generation of energy storage.
Case Studies: Improvements in Battery Performance Using Precision Grinding
Precision grinding has revolutionized battery materials, boosting their performance significantly. For example, researchers found grinding the cathode material to a finer texture enhanced the battery capacity. The small particles increased the surface area for chemical reactions, making the battery more efficient. Another case saw an improvement in the longevity of batteries by refining the anode materials. Finer particles resulted in reduced degradation over time, thus extending the battery’s life. Technological strides in precision grinding equipment have allowed for uniform particle sizes and tighter distributions, which are critical in battery production. These cases underscore the pivotal role precision grinding plays in the development of advanced, high-performing batteries.